The Essential Guide to Fittings and Lubrication in Modern Industry
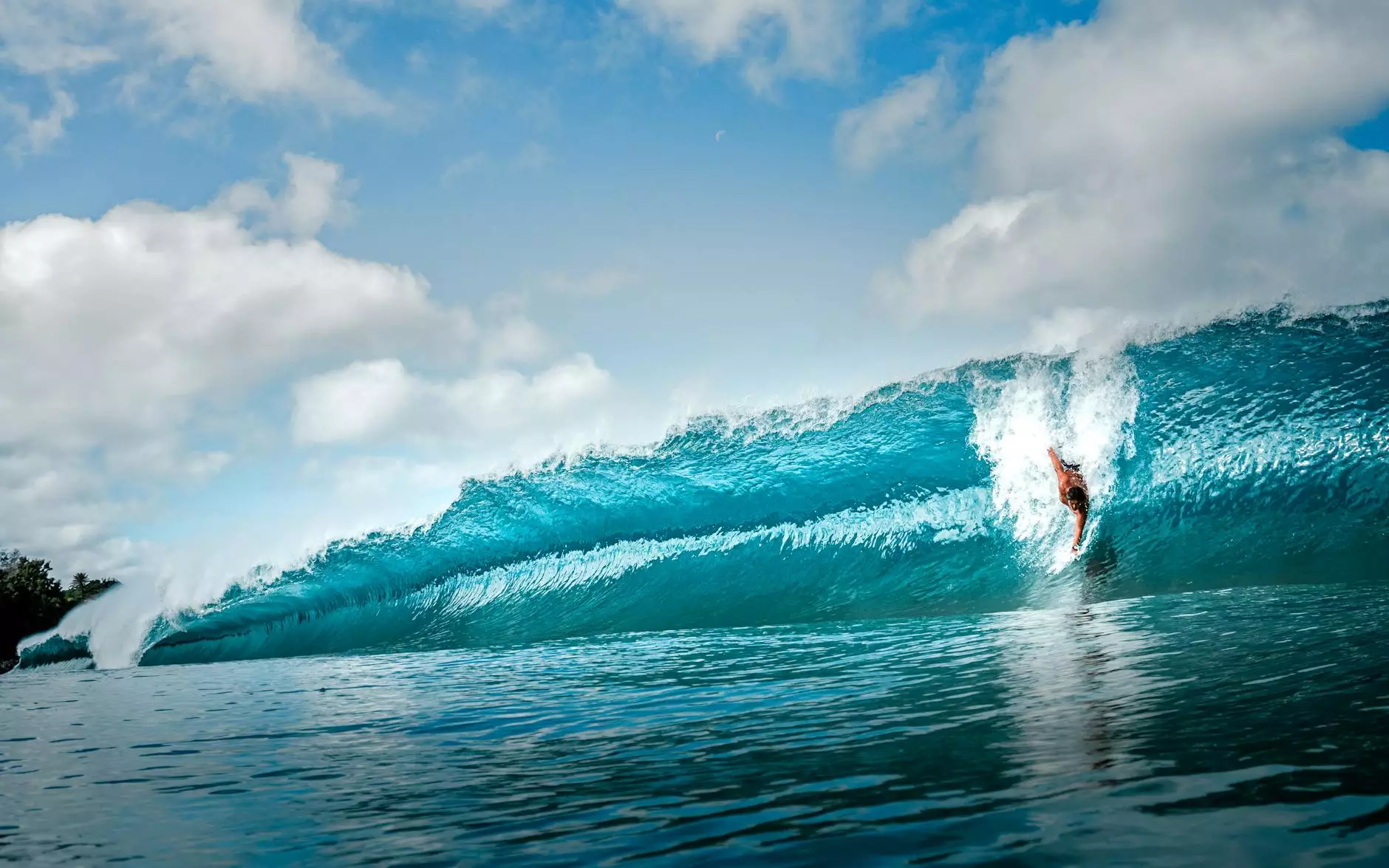
Understanding Fittings: The Backbone of Industrial Infrastructure
Fittings are essential components used in numerous applications across various industries. They play a pivotal role in establishing connections between different pipes, hoses, and tubes. Understanding their types, uses, and maintenance requirements is crucial for any business that relies on piping systems.
Types of Fittings
- Elbow Fittings: Used to change the direction of flow in pipes.
- Reducer Fittings: Allow connections between pipes of different diameters.
- Tees: Enable the branching of fluid flow into two directions.
- Couplings: Connect two pieces of pipe to ensure tight seals.
- Flanges: Facilitate easy joining and disassembling of piping systems.
The Importance of Proper Fitting Selection
Selecting the right fittings is critical to ensure the integrity and efficiency of piping systems. Incorrect fittings can lead to leaks, pressure drops, and ultimately costly downtime. Here are some factors to consider:
- Material Compatibility: Ensure that the fitting material is compatible with the fluid being transported.
- Pressure Ratings: Use fittings that can withstand the maximum pressure of the application.
- Temperature Limits: Ensure fittings can operate effectively within the required temperature range.
- Connection Types: Different applications may require threaded, welded, or flanged connections.
The Vital Role of Lubrication in Industrial Applications
Lubrication is often overlooked yet is an essential process that enhances the performance and lifespan of machinery and fittings. Adequate lubrication minimizes friction, reduces wear, and prevents overheating, leading to improved operational efficiency.
Types of Lubricants
Lubricants can be classified into several categories based on their composition:
- Oil-Based Lubricants: Fluid oils that offer excellent lubrication properties and are commonly used in engines and machinery.
- Greases: Thickened oils that stay in place and provide longer-lasting lubrication, ideal for high-load applications.
- Synthetic Lubricants: Man-made lubricants designed for extreme conditions, providing superior performance in harsh environments.
- Solid Lubricants: Such as graphite and molybdenum disulfide, used in applications where liquid lubricants cannot be employed.
Benefits of Effective Lubrication
Implementing a robust lubrication strategy offers numerous benefits:
- Reduced Wear: Minimizes wear on moving parts, extending their operational lifespan.
- Enhanced Efficiency: Lowers energy consumption by reducing friction between components.
- Temperature Control: Helps regulate the temperature of machinery, preventing overheating and potential failure.
- Corrosion Prevention: Protects metal components from oxidation and corrosion, ensuring longer service life.
Fittings and Lubrication: A Critical Relationship
The connection between fittings and lubrication is significant in achieving optimum performance and reliability in industrial systems. Proper lubrication of fittings can prevent seizing, enhance flow efficiency, and reduce maintenance costs. Here’s how to ensure this relationship remains effective:
Strategies for Effective Fitting Maintenance and Lubrication
- Regular Inspections: Conduct routine checks to identify wear and tear in fittings.
- Lubrication Schedules: Establish a lubrication schedule based on the manufacturer’s recommendations and operational demands.
- Quality Lubricants: Use high-quality lubricants that meet the specifications of your application for maximum efficiency.
- Environmental Considerations: Ensure that the lubrication method used does not adversely affect the environment, especially during handling.
Case Study: Fitting and Lubrication in Industrial Applications
Consider a manufacturing facility utilizing hydraulic systems that rely heavily on various fittings. By implementing a structured lubrication plan and selecting high-quality fittings from fitsch.cn, the facility can achieve significant improvements in operational performance:
Results
- Decrease in downtime due to fewer leaks and failures.
- Improvement in overall machinery efficiency.
- Extended lifespan of fittings and machinery components.
- Reduction in maintenance costs and resource consumption.
Best Practices for Choosing Fittings and Lubricants
To maintain high operational standards, businesses must adopt best practices in selecting the right fittings and lubricants:
Selection Criteria for Fittings
When selecting fittings, companies should consider the following criteria:
- Durability: Look for fittings that offer robust performance under varying conditions.
- Compatibility: Ensure fittings are compatible with your existing infrastructure and materials used.
- Manufacturer Reputation: Choose reputed manufacturers like fitsch.cn known for high-quality products.
- Cost Efficiency: Balance cost with quality to maximize the return on investment.
Lubrication Best Practices
Your lubrication strategy should include:
- Employee Training: Proper training for staff on lubrication processes and safety practices is crucial.
- Monitoring Systems: Implement monitoring systems to track lubrication levels and performance.
- Sustainability Practices: Adopt sustainable lubrication practices to minimize environmental impact.
Conclusion: Maximizing Efficiency with Fittings and Lubrication
Utilizing the right fittings in conjunction with effective lubrication practices is key to achieving operational excellence in any industrial environment. By focusing on quality, compatibility, and systematic maintenance strategies, businesses can ensure the integrity of their systems, reduce unexpected complications, and ultimately drive profitability. Trust in reliable providers like fitsch.cn for your fittings needs and embrace a comprehensive lubrication strategy to harness the full potential of your industrial operations.
fitting,lubrication