Prototyping Rubber Bellows: Revolutionizing Design and Engineering
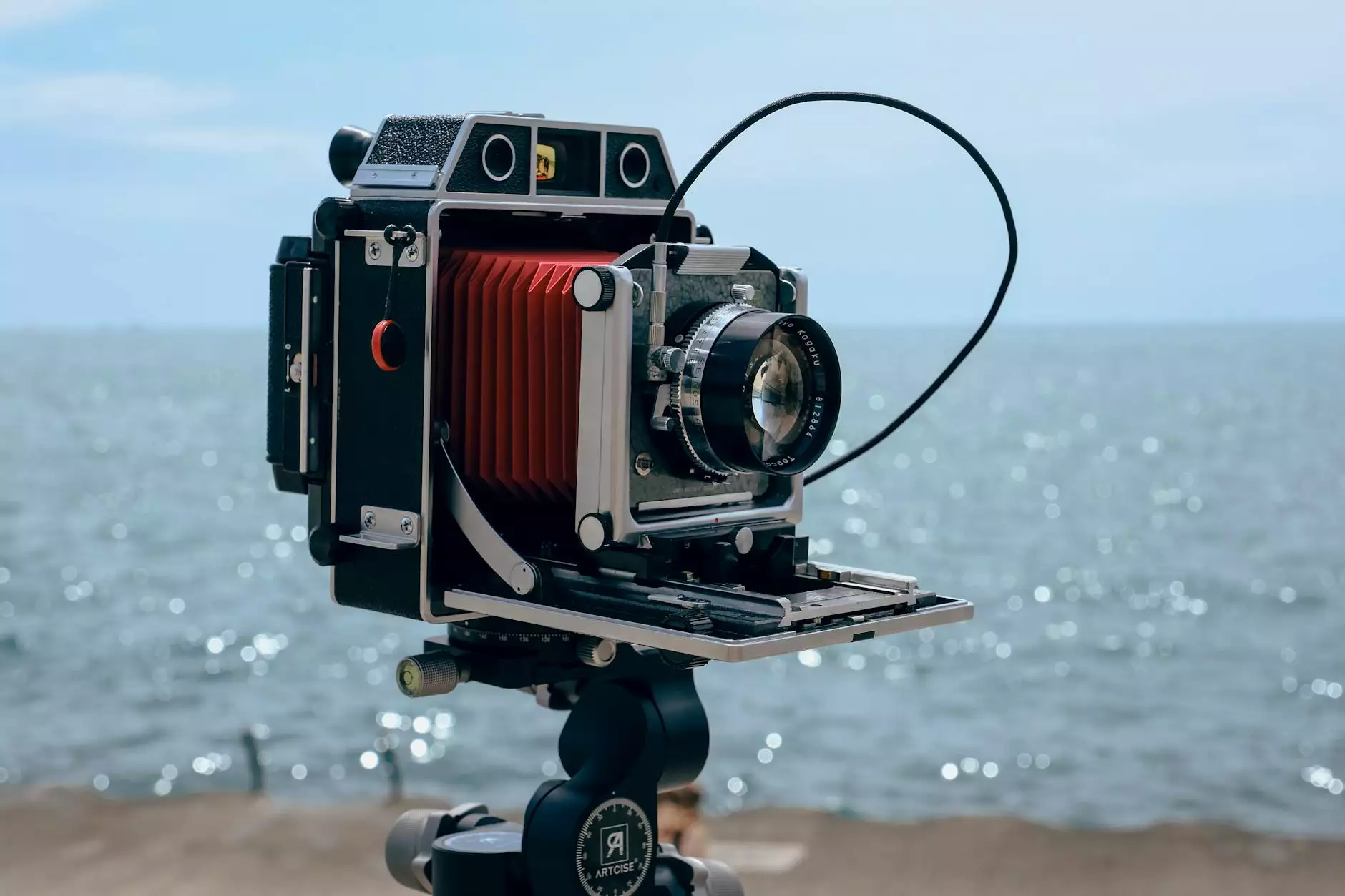
In the ever-evolving world of manufacturing and engineering, prototyping rubber bellows represents a significant advancement that bridges the gap between concept and reality. At Ovictor Group, we understand the profound impact that precision-designed rubber bellows can have on a variety of applications, enhancing both performance and durability. In this comprehensive article, we will delve into the intricacies of prototyping rubber bellows, examining their advantages, applications, and the innovative processes involved in their creation.
The Importance of Prototyping in Modern Manufacturing
Prototyping is an essential phase in the product development lifecycle. It allows designers and engineers to test their ideas in a tangible way before moving into full-scale production. The significance of rubber bellows in prototyping cannot be overstated—these components are critical for various applications, providing flexibility, adaptability, and reliability.
What Are Rubber Bellows?
Rubber bellows are flexible, expandable enclosures designed to permit relative movement and protect sensitive components from contaminants. Their design often incorporates a series of convolutions or folds, which enable them to compress and expand without losing integrity. This versatility makes them a favored choice across numerous industries.
Characteristics of Rubber Bellows
When discussing prototyping rubber bellows, it's important to address their key characteristics:
- Flexibility: Rubber allows for a wide range of movement, accommodating varying operational conditions.
- Resilience: High-quality rubber can withstand harsh environments, chemical exposures, and temperature variations.
- Customizability: Prototyping enables engineers to tailor bellows to specific dimensions and performance requirements.
Applications of Prototyping Rubber Bellows
Rubber bellows find applications in numerous industries, including:
- Aerospace: Protecting hydraulic lines and connectors from debris and environmental factors.
- Automotive: Providing protection for steering and suspension systems, as well as exhaust systems.
- Manufacturing: Used in robotic applications and machinery to absorb vibrations and movements.
- Medical Devices: Ensuring the integrity of sensitive instruments by sealing them from external contaminants.
Benefits of Using Prototyping Rubber Bellows
The prototyping process helps to validate designs and evaluate the performance of rubber bellows across different scenarios. Some of the key benefits include:
- Enhanced Performance Testing: Immediate feedback on the physical properties of rubber bellows under varying conditions.
- Cost Efficiency: Identifying potential design flaws early can significantly reduce material waste and production costs.
- Increased Innovation: Rapid prototyping encourages creativity, allowing engineers to explore unconventional designs and solutions.
The Prototyping Process for Rubber Bellows
The journey from concept to prototype involves several stages, each critical for achieving optimal results. Here’s a deep dive into the prototyping process specifically for rubber bellows:
1. Design Phase
In this initial phase, engineers collaborate to create detailed designs and specifications for the rubber bellows. This step involves:
- CAD Modeling: Utilizing computer-aided design (CAD) software to produce accurate models.
- Material Selection: Choosing the right type of rubber material based on the intended application and environmental factors.
2. 3D Printing Prototyping
One of the most transformative technologies for prototyping is 3D printing. This method provides several advantages:
- Speed: Rapid production allows for quick turnaround times, facilitating faster testing.
- Precision: Advanced 3D printers can create highly detailed prototypes that closely mimic the final product.
- Cost-Effectiveness: Reduces material costs and minimizes waste, making it an economical choice for prototyping.
3. Testing and Evaluation
Once the prototype is developed, rigorous testing procedures are undertaken to assess performance characteristics:
- Compression Tests: Evaluating how the bellows compress and expand under load.
- Environmental Testing: Ensuring the prototype withstands temperature fluctuations and exposure to chemicals.
- Durability Assessment: Testing for wear and tear over time to ensure longevity and reliability.
4. Iteration and Refinement
Based on the feedback from testing, necessary modifications to the prototype are made. This iterative process is crucial for optimizing the design and ensuring that the final product exceeds performance expectations.
Challenges in Prototyping Rubber Bellows
While prototyping offers immense benefits, it is not without its challenges. Some of the issues that engineers may face include:
- Material Limitations: Different rubber compounds can behave unpredictably under various conditions, which may complicate the design process.
- Complex Geometry: Achieving the desired shape and functionality may require advanced techniques, especially for intricate designs.
- Cost of Prototyping: Depending on the materials and methods used, the prototyping phase can be costly if not carefully managed.
Conclusion: Embracing the Future with Prototyping Rubber Bellows
As we navigate through the complexities of product development, the role of prototyping rubber bellows is becoming ever more critical. By leveraging advanced design techniques and innovative materials, businesses are not only improving their product offerings but also ensuring an enhanced experience for end users.
At Ovictor Group, we are committed to advancing the field of rubber bellows design and prototyping. Through our state-of-the-art facilities and expert knowledge, we enable industries to harness the full potential of their designs, ultimately driving innovation and efficiency.
Contact Us for Your Prototyping Needs
Ready to take your designs to the next level? Contact Ovictor Group today to learn more about how our expertise in prototyping rubber bellows can transform your projects. Our dedication to quality and precision ensures that you receive the best possible prototype, tailored to your specific needs.